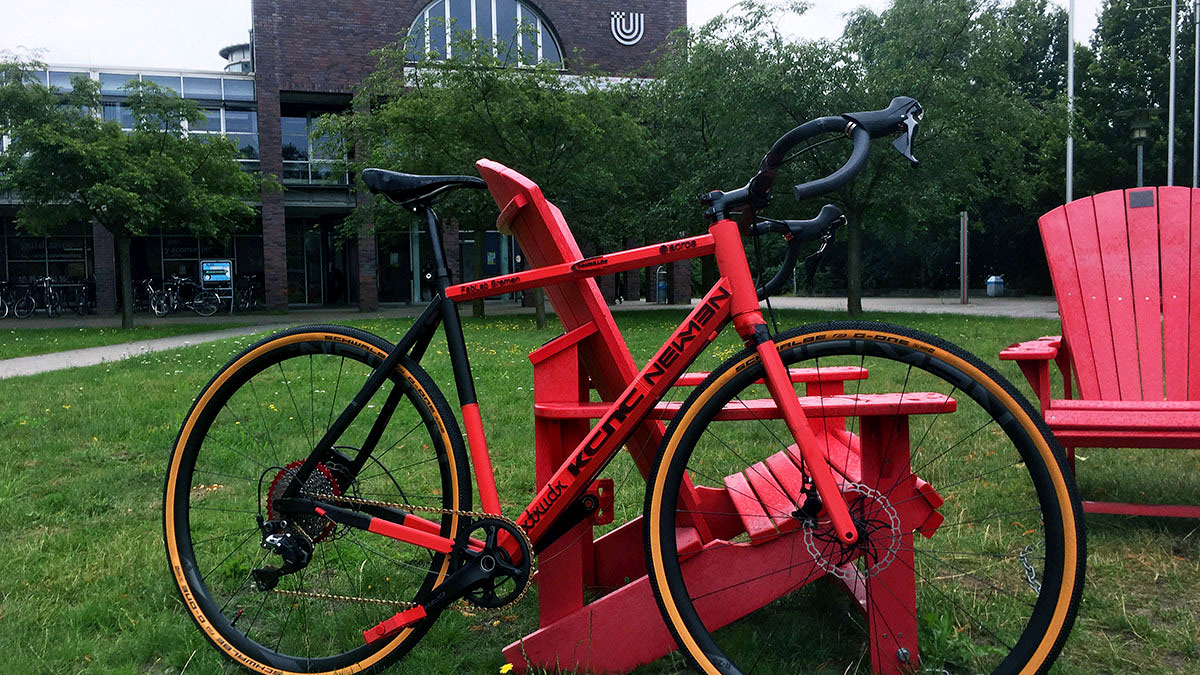
© Till Kolligs
The Printed Bicycle
Students produce a bicycle with a 3D printer
What does the future of the bicycle look like? If you ask the group of students surrounding Till Kolligs you’ll hear: It must be light, sustainable, and not too expensive. They not only developed a design in Bremen’s FabLab but also printed the bicycle with a common 3D printer.
The new possibilities that a 3D printer bring with it have fascinated Till Kolligs and his housemate for a long time. Together with three other students from the University of Bremen, they pondered over the future of bicycle production for over half a year. How can you produce a light, sustainable, and yet affordable bicycle? And how can you do it without steel, aluminum, or carbon?
A Light, Ergonomic Bicycle for the City
The students from the fields of sociology, digital media, and production technology first of all took a closer look at the city for their planning. “Bremen is a very bicycle-friendly city,” determined Till Kolligs. “The high proportion of bicycle traffic is politically desired and promoted.” However, there are challenges facing bicycle owners – especially in the city center. There are a lack of secure places to park your bike resulting in some citizens carrying their bikes up and down stairs several times a day. Additionally, the ergonomics of many bikes are not fitted to their riders enough.
“We should therefore be able to square the circle in designing a bicycle that can be individualized with regards to its geometry, that is light so that it can be carried well, and is also affordable and sustainable,” states Kolligs. Especially the sustainability aspect should not fall short. Common materials such as steel and aluminum require a great deal of energy during production and endanger the existence of rainforests purely by means of extraction. The technology that promises to make this wish possible is 3D printing.”
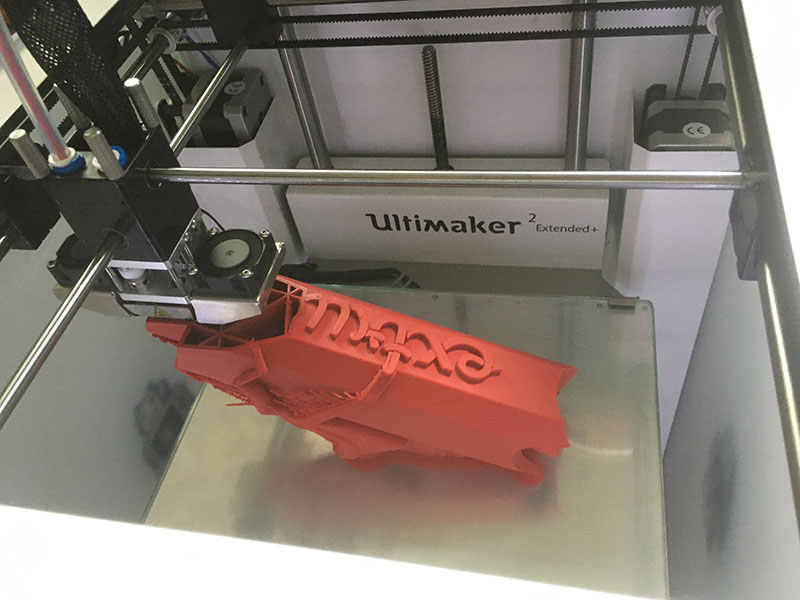
© Till Kolligs
The next step involved the detailed planning and material research. It quickly became clear that not all components can be printed. Amongst other parts, the tires, chain, and brakes come from external suppliers. “The production of the stated components would be completely individual projects,” reveals Kolligs. “That is why we have initially concentrated on the production of the frame.” In order to ensure that the bicycle was still roadworthy in the end, the group was supported by many companies. For example, NEWMEN, who provided one of their lightweight wheel sets, KCNC, who sponsored the cassette, chain, and disc brakes, as well as Acros and Schwalbe.
The requirements for the material were high: A bike must be stable and be able to withstand great strain. In the end, the group found the filament manufacturer Extrudr in Austria, where the autonomously developed material GreenTec Pro is available. “The material has a good bending strength and can withstand external impact. Moreover, it is biodegradable under specific circumstances and is not produced with crude oil – that was very important to us,” explains Kolligs.
One challenge was the print planning: The group was able to use a high-precision 3D printer at the FabLab at the University of Bremen. However, the printer only has a constructional space of 223 mm x 223 mm. Thus, the frame had to be printed in several parts. The design also had to be compatible with the parts that were not able to be printed.
How Do You Print a Frame?
The bike that is to be printed should be a gravel bike – an off-road model with a diamond-shape frame. After the computer modelling, the first test prints and a tensile test were carried out to determine the printing parameters. “Subsequently, there were incorrect prints and improvements,” states Kolligs. “We had nearly used up all of the available material that we had by the time we printed the final model.” After the last print, the team faced the biggest challenge yet: Connecting the individual parts to make a frame.
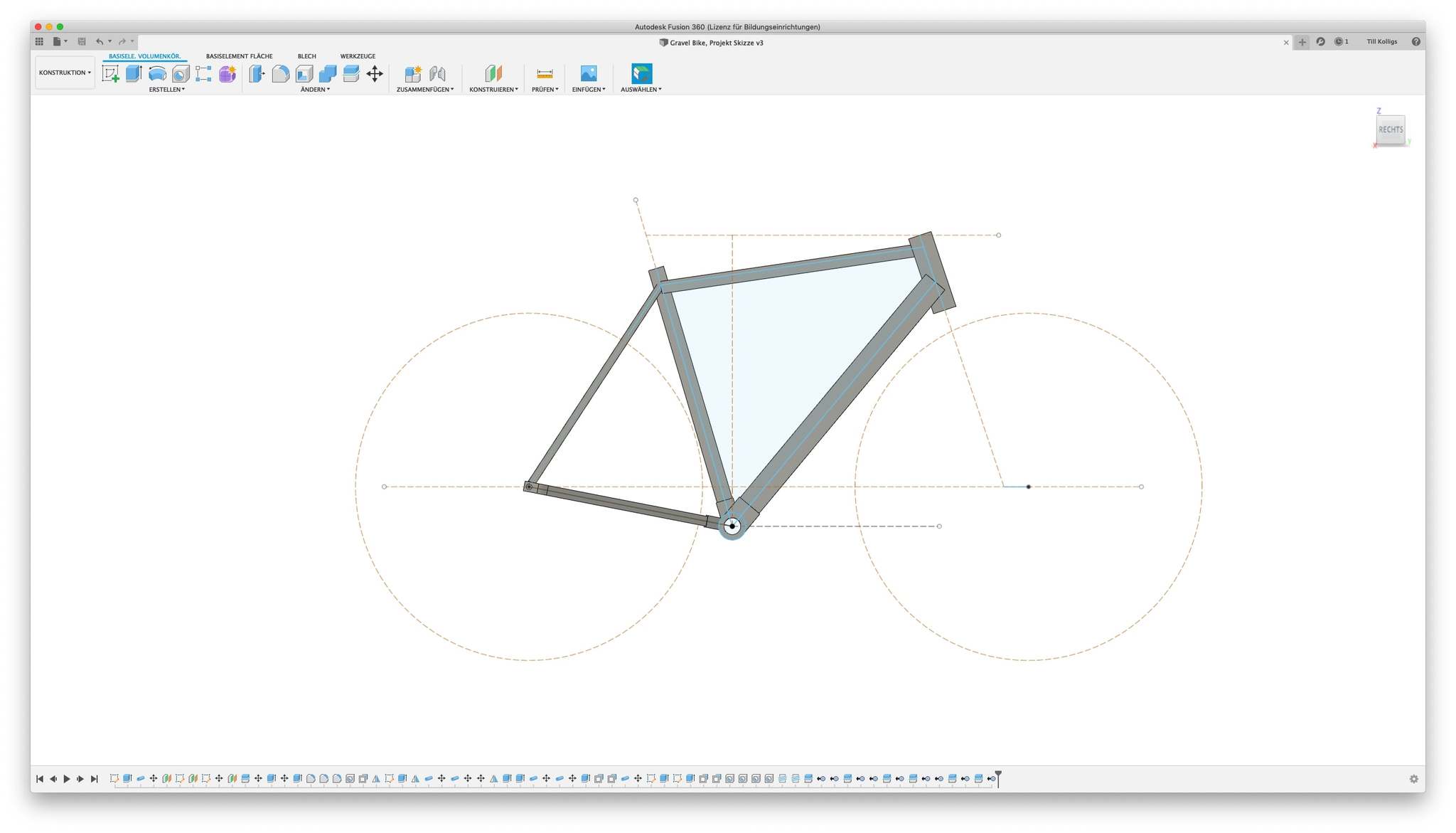
© Till Kolligs
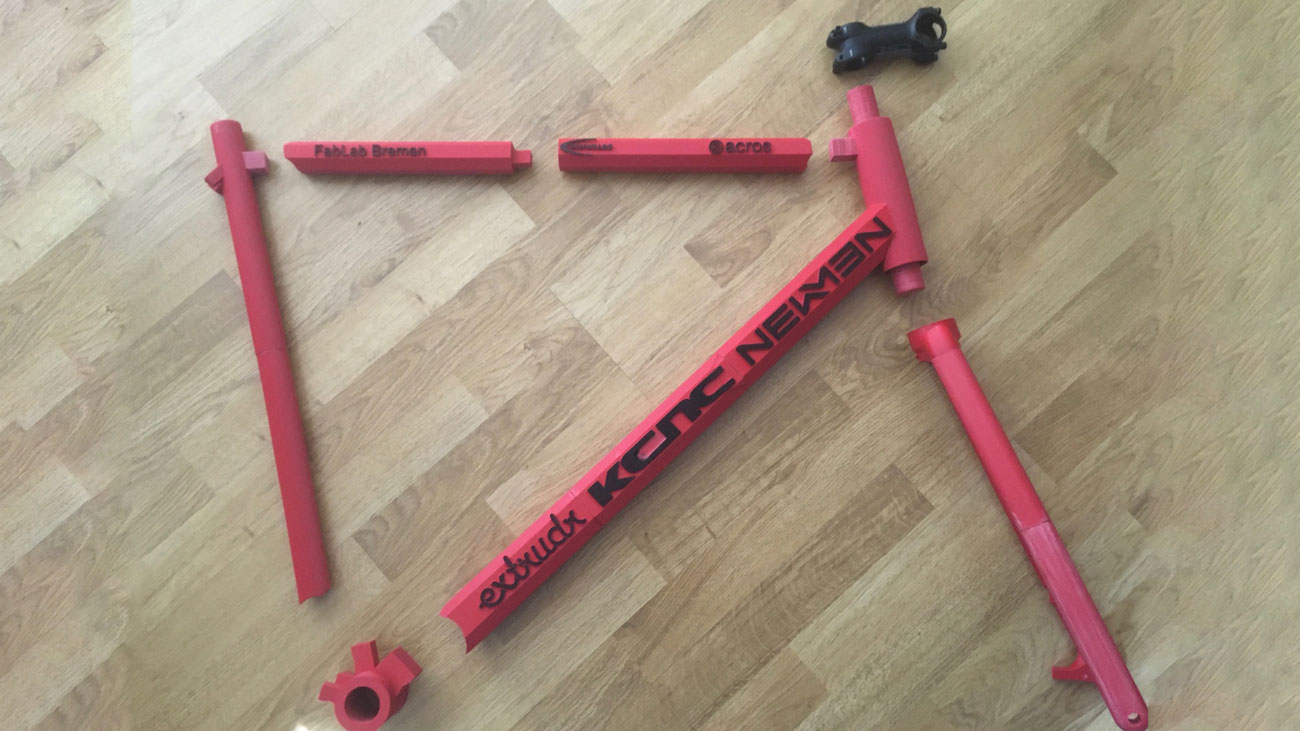
© Till Kolligs
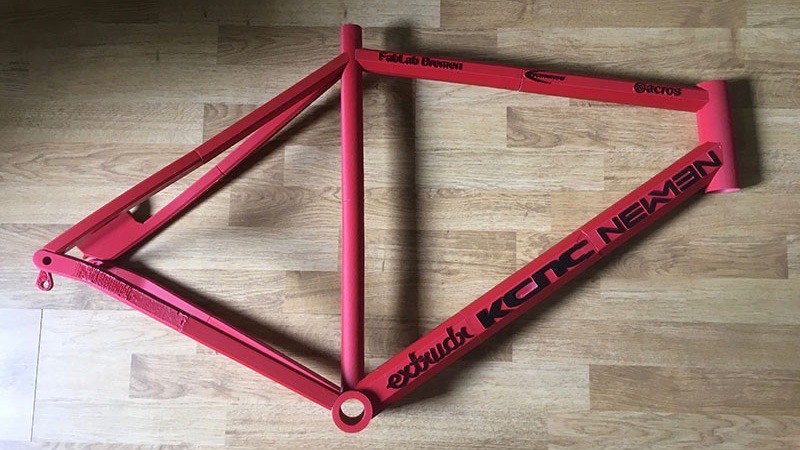
© Till Kolligs
“I would have been optimal to connect the printed parts by means of high-frequency welding,” states Kolligs. “But we didn’t have the machine for that. So we experimented with plug connections and PVC adhesive. However, we ended up working with two-component epoxy resin adhesive. Epoxy resin adhesive is one of the strongest forms of glue under certain circumstances but it is unfortunately not perfect four our needs. Much like with an aluminum frame, the connections have become the weak spots of the frame.”
The First Test Ride
Yet the bicycle was still completed: “The final frame – even if it still is a prototype - was indeed created with many hours of thinking, much sweat, frustration, and patience. The moment when we were in fact able to attach all parts to the frame, everything fit, the brakes didn’t grind, and we were able to smoothly change gear was amazing,” reports Kolligs.
“All the hard work was worth it. Despite the fact that we placed our focus on stability and not on the weight, the finalized frame only weighed 1450 grams, the fork only 350 g. Additionally, the bike can easily be fitted to other body sizes with the computer. The first time sitting on the bike was an exciting moment – the frame remained stable. The problem was not really the frame itself but the fork that buckled slightly when the bicycle first rolled. The fork couldn’t withstand any real weight and one glued connection broke, where the load was the highest, when a test braking manoeuvre was carried out. Our next step will be to print the fork in one piece with a bigger printer and also make it thicker.”
The team is still happy: “We have shown that you can indeed reinvent the wheel” – or in this case the bicycle. The prototype shows that it is generally possible to produce durable bikes with a 3D printer. “Even if the project did take up a lot of time, we are really happy that we started it. The University Bremen and the FabLab gave us the opportunity to turn an initially crazy-sounding idea into reality!”
About the FabLab
The FabLab (Fabrication Laboratory) is a place where school pupils, students, and teaching staff have the chance to experiment with technologies and materials and also learn during the production process (“learning-by-design”). 3D printers, vinyl plotters, and Arduino technology, to name a few examples, are implemented to promote the creative usage of technology and to make it understandable. The FabLab is operated by the Digital Media in Education (dimeb) working group from the Faculty of Mathematics / Computer Science at the University of Bremen.